In a boost for sustainability, the University of Leoben’s latest meta-study confirms that plastic pipes (both pressure and non-pressure) can last for over 100 years. With this durability confirmed, it’s time to shift focus to the next big question: how can we build on this longevity and accelerate the uptake and lifespan of pipes made with recycled plastics?
We talked with Standardization and Certification Manager, Jeannette Mulder, to find out.
Analysis that closes the longevity debate
For those not immersed in the technicalities of plastic pipe construction and testing, this meta-study — commissioned by the prestigious European Plastic Pipes and Fittings Association (TEPPFA) — is a helpful summary of research to date. It brings together findings from 49 published sources to confirm that plastic pipes used underground to transport sewage and wastewater can be relied upon for over a century.
However, this debate was concluded a while ago for experts like Jeannette Mulder and the Wavin (an Orbia business) team. At their times of publication, all the studies included in the meta-study showed that pipes examined over the years covered by these earlier studies, and following the adjustments made during standardization, had properties able to last a long time.
Widening the use of circular raw materials in plastic pipes
Speaking with Jeannette Mulder about the meta-study, it’s clear that it’s a valuable springboard to further research and exploration. Wavin teams have spent many years on research, allowing our business to forge ahead as innovators in the plastic pipe and fittings sector. We’re already undertaking advanced work to create more sustainable solutions by manufacturing high-quality products from recycled materials. A critical part of this will be working alongside leading organisations, like TEPPFA, to help develop specific standardized testing for pipes containing recycled materials.
At Wavin, we’ve been working with recyclates for decades and have developed a respected range of low-carbon pipes and fittings of quality equal to those made from virgin materials. This tried-and-tested range is popular with customers and offers an effective route to reducing the Global Warming Potential (GWP) of building projects and increasing overall sustainability.
Adopting these solutions will enhance industry-wide sustainability, but to widen the market for recycled and low-carbon pipes, it will be essential to demonstrate their consistent quality through specific tests that assess the particular characteristics of pipes containing recycled materials.
Jeannette Mulder is committed to establishing these industry-wide standardized tests, specifically when used in non-pressure applications. Although this process may have challenging aspects, she’s confident that, through collaboration, the industry can overcome them to advance the testing of recycled pipes:
“The meta-study findings confirm that current testing standards are appropriate and reliable for virgin plastic and don’t need to change. However, the makeup of plastic piping is changing to include recycled materials in some products (especially for non-pressure use). In light of these changes, there are opportunities to advance the robust testing standards already in place. Ideally, the industry will collaboratively and carefully update standards and methodologies to preserve the longevity and quality of plastic pipes when recycled materials are involved, and when dealing with material resources less consistent than virgin materials.”
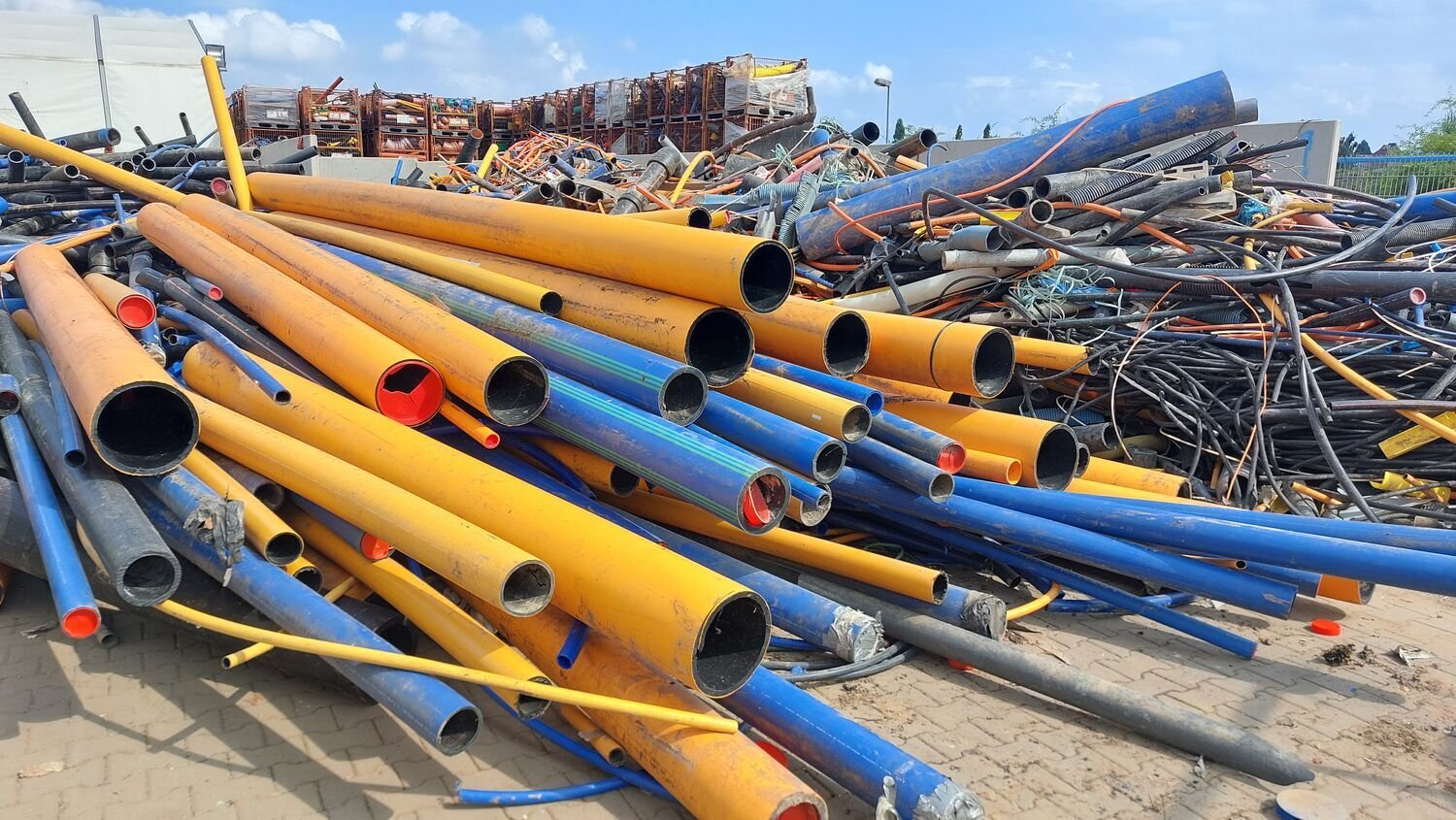
Why plastic pipes outperform concrete alternatives
Wavin’s low-carbon multi-layer PVC pipes already perform precisely as pipes made from virgin materials do.
Plastic pipes, including recycled pipes, perform more reliably than concrete alternatives, which tend to be more friable and rigid. Plastic pipes also demonstrate greater resistance to pipe creep and deformation under high loads. Additionally, unlike concrete pipes, where any movement can cause a break, plastic pipes tend to remain stable thanks to greater flexibility, which is also why they’re less likely to suffer damage if dropped or mishandled.
Even concerns like the possibility of oxidation due to exposure to chemicals or UV light can now be set aside, as the meta-study confirmed the efficacy of stabilizers included in the interior of plastic pipes. Several papers that contributed to the TEPPFA study detected the presence of stabilizers in plastic pipes, even after decades of service.
Pressure to create adapted standards for pipes containing recycled materials
We fully support the market desire for high-quality plastic pipes and fittings that perform efficiently for up to 100 years. However, as experts like Jeannette Mulder point out, recycled pipes are currently exclusively tested using methodologies developed for virgin plastic pipes. These robust standards have served the plastics industry well for many years, but as recycled materials become increasingly important, it’s appropriate that this shift is reflected in updated standards and testing methodologies.
When it comes to practical quality control, adopting the same testing standards used for virgin pipes may not be the best long-term approach. For example, she highlights the need to consider additional factors in testing, such as the more significant variability that occurs when plastic pipes include recycled material content. Recycled feedstock isn’t as uniform as virgin feedstock, so achieving constant material performance is more challenging. It’s an exciting area of development and one that Wavin will actively contribute to through the many working groups and ongoing studies taking place around the world.
Product standards used for testing are a key starting point as we begin developing tests specifically designed for recycled materials:
- The biggest challenge for pressurized pipes is cracking due to internal pressure. If a pipe contains minor flaws and full pressure is applied, stress cracking may occur, and if those cracks grow, they can lead to leaks. For low-carbon materials used in these situations, chemically recycled inputs are a good option next to using the currently permitted allowance of recyclates of pipe materials (with known properties).
- There’s a balanced argument for developing test methods that more closely reflect the uses of non-pressurized pipes. Although recycled non-pressure pipes aren’t used in pressurized situations, they’re currently subject to tests designed for pressurized virgin pipes. Taking into account the final use of the pipe instead will be an important first step towards creating test methods specific to recyclates.
This change in direction is one TEPPFA highlights in the meta-study. It points out that evolving current pipe test methods will help ensure they’re the best fit for determining the lifespan of non-pressure pipes.
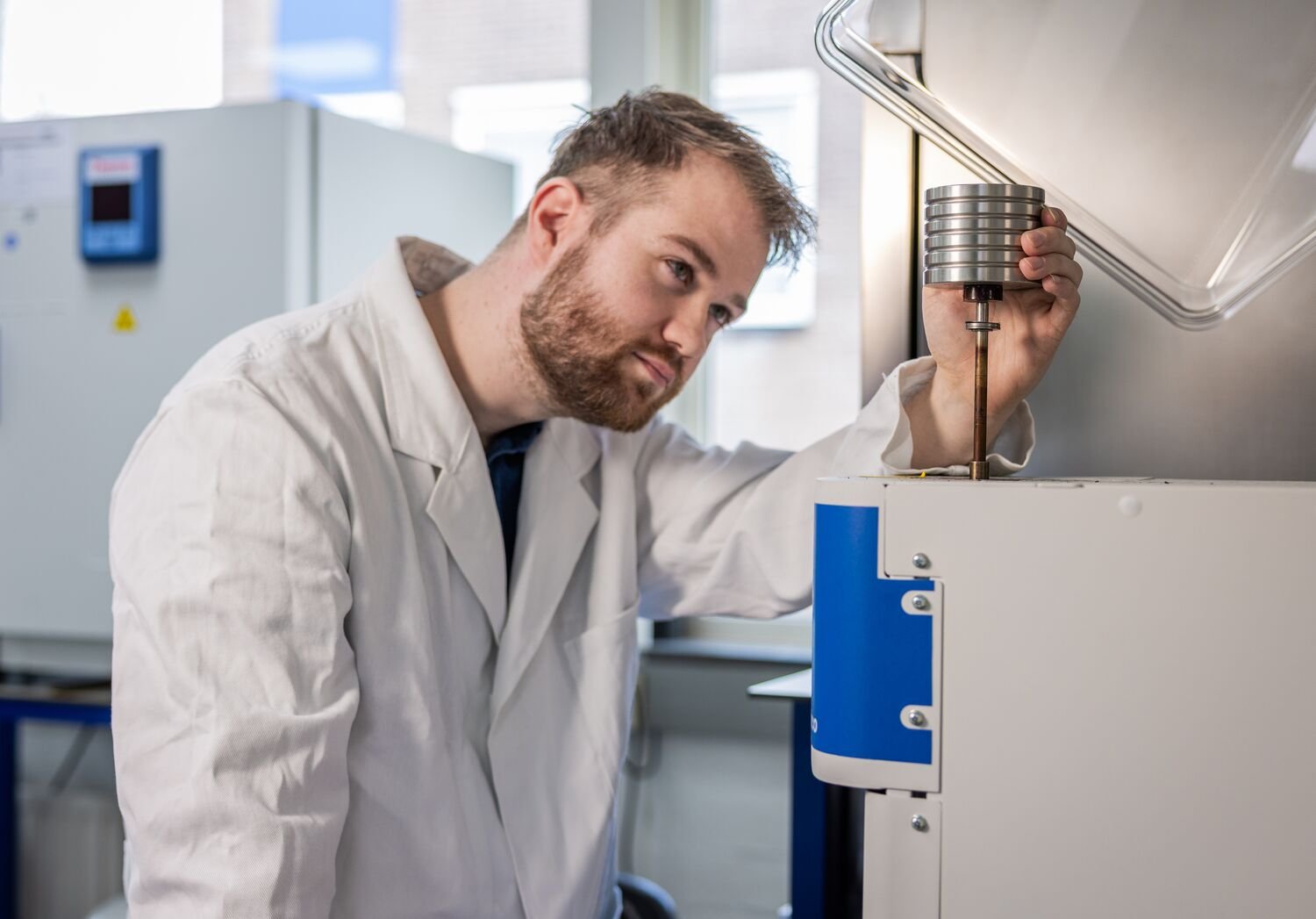
The direction of future standards
At Wavin, we’re eager to drive sustainability forward. We see the development of more applicable standards as an important step toward achieving this goal.
In parallel, Jeannette Mulder suggests that future pipe development should look beyond design and material requirements and emphasize a pipe’s application when determining specifications.
She cites the impact of ground settling as a prime demonstration of how a pipe's longevity isn't solely defined by its material strength or design; the stability and characteristics of the external environment also influence it. For example, non-pressurized sewer pipes experience maximum external pressure from ground loads within the first two years after installation as the ground settles. However, once settled, the ground forms a strong support around the pipe, shouldering most of the load and almost wiping out any further risk of stress or damage.
Should this become a more prominent factor in pipe specification, there would be more scope to amend other design elements to shape the product to the application. We support the broader development of standards representing the likely applications of pipes and welcome opportunities to contribute to this work.
How we’re advancing testing and development of low-carbon pipes and fittings
Helpfully, the meta-study also confirms our long-held understanding that non-pressure pipes made with circular raw materials are just as strong as those made with virgin materials. Decades before the study was published, our commitment to high-quality products drove us to test and verify this ourselves thoroughly. Our accredited facility ensures that our blend of virgin and recycled materials matches the strength of entirely virgin pipes. And we never compromise on quality.
Our Recycore® Technology, for example, uses as much recycled material as possible to ensure that products have the same or better proven and excellent performance characteristics as the virgin products they replace. To illustrate this point, Recycore Technology 110mm and 160mm drain and soil pipes have been extensively and independently tested, and their performance is standardized to EN1453-1:2017 and EN 13476. Their characteristics are identical to those required for solid wall pipes by EN 1401-1:2009 and EN 1329-1:2020, respectively.
Standardization workgroups are now opening the standards up to accommodate the assessment of 100% recyclates (coming from different sources) while keeping the current requirements and test methods, knowing that it might not be possible for every recyclate material to apply to meet the standards. The next step will be to generate more opportunities for progress through industry-wide collaboration and research to further develop standards and testing without compromising quality.
Striding towards a more sustainable future
This is an exciting time for pipe innovation. As the frontier of recycled plastic pipes and fittings forges ahead, we look forward to being at the forefront of high-quality product development and contributing to the adoption of standards reflecting the increased use of recycled plastics.
To learn more about our sustainability achievements and how we’re incorporating recycled materials into our solutions, visit our dedicated webpage.
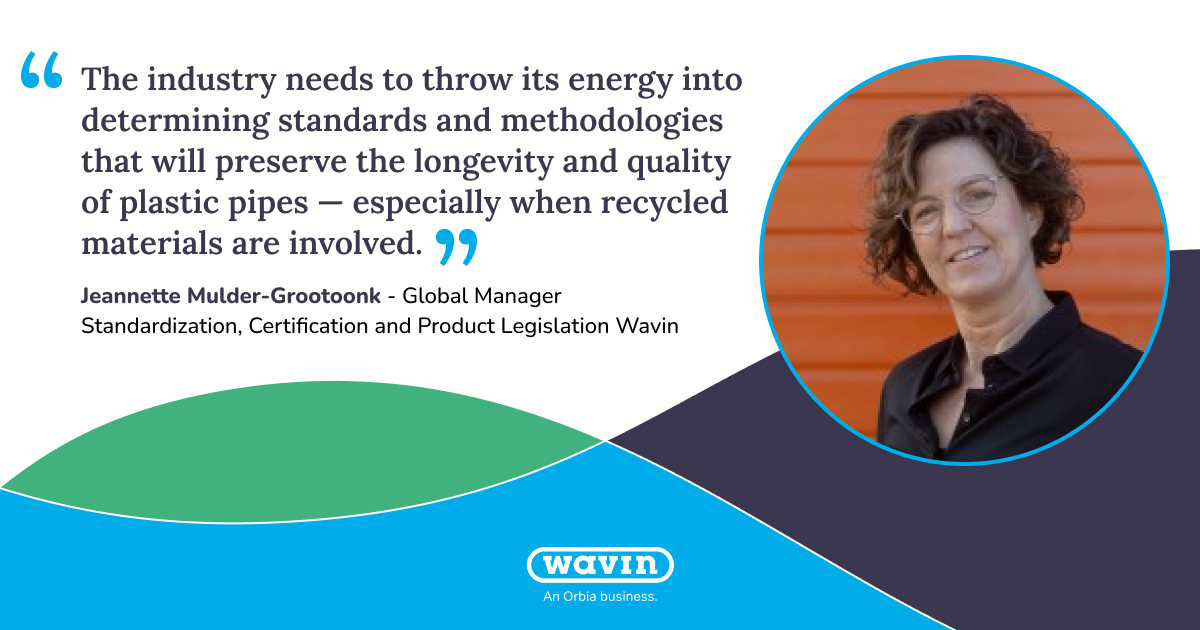
We also interviewed Maarten Hamberg (Senior Technology Manager) and Ronald Bal (Global Circularity Manager) about the TEPPFA meta-study. Be sure to read their perspectives as well.